Bekijk het origineel
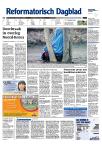
Bekijk het origineel
Draaien zonder tandwielkast
Nederlandse windmolenfabrikant onderscheidt zich met "direct-drivetechnologie"
Nederland staat met onderzoek naar windenergie wereldwijd gezien aan de top, aldus een recent rapport van de Europese Unie. Als het echter om het bouwen van de apparaten gaat, lijkt juist het land van de molens de boot gemist te hebben. Diverse kleine bedrijven proberen nu steekjes op te pakken die de buitenlandse giganten laten vallen. Ze bouwen stuk voor stuk voort op de technologie van de failliete bouwer Lagerwey Windturbines, bekend van de blauwe tweewiekers.
Premium Artikel
Dit artikel is exclusief leesbaar voor abonnees met een RD-abonnement, een zesdaags abonnement op het RD of op de e-paper. Dit artikel lezen? Log in op uw EMG-account of neem een abonnement.
Inloggen Neem (proef)abonnementBekijk de hele uitgave van dinsdag 13 februari 2007
Reformatorisch Dagblad | 20 Pagina's
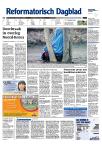
Bekijk de hele uitgave van dinsdag 13 februari 2007
Reformatorisch Dagblad | 20 Pagina's